Refleks Heater
After doing a lot of research I what kind of heater we needed on the Far Reach I decided on the Refleks Model 66MK. It has a superb reputation for reliability and heat output. The cast iron top and 90 degree elbow is supposed to increase the amount of heat that it radiates. I had it made to operate off of kerosene since I don't plan to carry any diesel fuel. Propane heater are convient and put out a lot of heat but they use way to much fuel.
I initially thought I would get a larger model but it wouldn't fit in the space I had and then I received an email from Beth Leonard who suggested the model 66 would be a very good size for our boat. That piece of advice solved a lot of problems.
I ordered it with an elbow so I could determine how big the space would need to be to accommodate it. The elbow was about 4" long and as you can see in the top photo it stuck out much too far. All it did was make the footprint bigger. I needed to cut it off but I don't have a miter box. I looked at Lowes but the miter boxes they had were too expensive or cheap plastic. So, I built my own from some scrap 3/4" ply. I made it just wide enough to hold the pipe. I used drywall screws as fasteners and a jigsaw to make the narrow kerf so my hacksaw would not drift around while I mad the cut. Once I determined where the elbow needed to be cut I wrapped some tape around it and marked it. I inserted some doorshim wedges to keep the pipe firmly in place while I made the cut. I clamped the miter box to my out-feed table at the end of my table saw. I used a hacksaw blade I only use for cutting SS. I am very pleased with the cut--it came out nice and straight. I cleaned up the edges with a half-round file. Then I inserted it on the Refleks flue to check for fit. Perfect. I will set it aside for now and once the cleat installation is complete I'll use the Refleks to determine the footprint necessary to rough in a custom built space just forward of the starboard settee.
I initially thought I would get a larger model but it wouldn't fit in the space I had and then I received an email from Beth Leonard who suggested the model 66 would be a very good size for our boat. That piece of advice solved a lot of problems.
I ordered it with an elbow so I could determine how big the space would need to be to accommodate it. The elbow was about 4" long and as you can see in the top photo it stuck out much too far. All it did was make the footprint bigger. I needed to cut it off but I don't have a miter box. I looked at Lowes but the miter boxes they had were too expensive or cheap plastic. So, I built my own from some scrap 3/4" ply. I made it just wide enough to hold the pipe. I used drywall screws as fasteners and a jigsaw to make the narrow kerf so my hacksaw would not drift around while I mad the cut. Once I determined where the elbow needed to be cut I wrapped some tape around it and marked it. I inserted some doorshim wedges to keep the pipe firmly in place while I made the cut. I clamped the miter box to my out-feed table at the end of my table saw. I used a hacksaw blade I only use for cutting SS. I am very pleased with the cut--it came out nice and straight. I cleaned up the edges with a half-round file. Then I inserted it on the Refleks flue to check for fit. Perfect. I will set it aside for now and once the cleat installation is complete I'll use the Refleks to determine the footprint necessary to rough in a custom built space just forward of the starboard settee.
Refleks Heater Model 66MK with an excessively long elbow.
Elbow trimmed to within 1/2" of sea rail.
Task specific miter box--the cut is almost complete.
Top view. Door shim wedges kept the pipe from moving.
1 7/8" removed from the 90 degree elbow.
As part of the insulation project I also needed to make a decision where the hole for the kerosene heater flue would need to be cut in the cabin top. I could not do that with out having the two 45 degree elbows that will ultimately determine how far I could off-set the vertical part of the flue pipe. So, I ordered the two elbows from Hamilton Marine in Maine. To prepare for the arrival of the 45 degree pipes I needed install a temporary shelf for the heater. I began by installing 1"X1" mohogany cleats on the bulkheads that will hold the platform that the Refleks heater sits on. I made a template out of doorskin ply and hot glue and cut a temporary piece of 1/2" ply for the shelf. The actual shelf will be Black Walnut, same as the cabin sole. I used a thin batten to trace a gentle curve for the inboard edge to see if liked the diagram I drew last year. Satisfied with the curve I made the cut with a jig saw and installed the temporary shelf. There will eventually be A. Mahogany vertical v-groove staving as the face panel below the shelf that will be removable allowing me to access the heater fuel overflow tank installed below the heater as recommended by Refleks.
I started work on installing the deck flange for the Refleks kerosene heater. First I removed the overhead panel where the flue will pass through the overhead. Then, I used a pump bob to decide exactly where the center of the flue would be located. I drilled a 1/8" hole. On deck I measured how tall the teak "riser" would need to be to accommodate the slope of the deck--about 1 7/8" over a width of about 7 1/2". After that, I cut three piece of teak so they would measure 8"x8" and 1" thick. When stacked they would be three inches thick. I decided to use resorcinol glue. To my knowledge it is the only 100 percent waterproof and UV resistant glue made. Unlike epoxy, it can withstand very high temperatures before it looses it's strength. I like epoxy. I have used a lot of it. But, I have seen some problems with it when exposed to high temperatures. Larry Pardey wrote an excellent piece discussing adhesives in his book, "Classic Boat Construction: The Hull." It's a great resource. Anyway, it took about a year to run down the resorcinol I wanted--called Aerodux 185. It is sold by C.P Adhesives. It is a cold weather resorcinol (down to 50 degrees I think) and fillers can be added to make it gap filling. Many other resorcinols will not accommodate fillers. Anyway, I used it for the first time for this project. After I cut the teak I sanded it with 120 grit paper to remove residues. I wiped it with acetone. I mixed up the resorcinol (it must be weighed) 5:1 liquid to the powder activator. I used a small kitchen food scale to weigh the parts. I brushed it on both sides for each of the two joints and clamped it firmly. I left it over night. The next day I removed the clamps and used a compass to draw the circle necessary to support the flue pipe deck flange. I took the glued teak to the Camp Lejeune Base Wood Hobby Shop as they have a couple of band saws. I set up the saw to cut a five degree bevel. It took about 5 min to cut out the part. I cleaned it up on a very large bench sander. In the next few days I will cut the 4 3/4" diameter hole through the middle and begin shaping the under side to match the camber in the deck.
Below:
1. Determining where the flue hole needs to be drilled.
2. The teak to be glued up.
3. This is what the resorcinol looks like when spread on one side.
4. Clamped up and left over night.
5. The teak ring cut from the laminated layers of teak.
It was time to start working on the flue for the Refleks Type 66MK kerosene heater. I originally ordered a deck flange with a 9 degree bevel thinking that would make for an easier fit but the deck crown is more like 13 degrees where the flue needs to be located and the mismatch caused complications I did not want to deal with. So I sent it back to Hamilton Marine for a zero degree bevel deck flange--the deck flange is perpendicular to the flue. But, the one they replaced it with looked like it had been cut with a can opener. I am not a fan of SS but sometimes you have to compromise.
This the way the deck flange came from Refleks and Hamilton Marine. It looks like it was cut out with a can opener.
A couple hours of work with a mill file, sand paper, buffing compound and buffing wheel.
The bronze one I wanted was about $400 from Navigator Stove works and required a bigger hole. But, I expected a better finish on the Refleks product. I called Hamilton Marine, where I purchased the part. I emailed them photos. They basically said that all the round ones from Refleks are like that. Not true . . . the 9 degree beveled one was perfectly smooth--I sent pictures of it to Hamilton Marine. They were polite and offered to exchange it and pay for the shipping but the ones they had in stock were not any better than what I had. I sent photos to Refleks and they basically said, "All the ones we have look like that too." Fine, I took a mill file to it and filed the points smooth. Then, I sanded it with 120 to 320 grit. Then I hit it with a high speed sisal wheel and finished it off with some polish on a high speed buffing wheel. Much better. It looks just fine.
Next, I went back to work on the trim ring. As detailed in a previous post, I cut the trim ring from the square lamination I made on a band saw. Now I needed to cut a 4 3/4" hole through the trim ring for the deck flange to plug into. I hate buying one time tools. But there was no reasonable way around it. I bought a Lenox 4 3/4" hole saw. I saved a few dollars as it came without the arbor but since all my other hole saws are Lenox I was able to use the arbor from one of them. I decided I needed to cut the hole before I beveled the trim ring to match the deck. It was the only way to ensure it would be vertical. It took a while but I was able to cut it on my bench top drill press. First I drilled a 1/4" hole al the way through the center and out the other side. Then I used the hole saw to cut half way through the plug--all the way to the bottom of the hole saw. I flipped the plug over and using the 1/4" hole as a guide I cut back through all the way to the bottom of the hole saw which just made it through. A perfect hole. Next, I took the trim ring up to the boat and used some wood scraps to prop the outside edge up so that it was level on top. I then scribed around it with a compass. I used a power planer to cut most of the excess away. Then, I used a block plane and spoke shave to trim to the scribed line. It fit perfect. I was pleased. It made me realize how much I have learned during the rebuild as the did not require days of research and planning . . . it took maybe 45 min. Next, I took the hole saw up to the boat and after taping off the area I needed to cut through (to protect the gelcoat) I cut a matching 4 3/4" hole through the cabin top. I checked the fit of the trim ring over the hole. They lined up perfectly. I finished up the day by rounding over the top and inside edge of the trim ring with the router. Next day, I cut a caulking grove in the bottom of the trim ring to provide a place for caulk to lay and not get completely squeezed out. I developed a couple of options for securing the trim ring to the cabin top. In the end I went with the simplest of the options as suggested by someone I trust. I used 3M 4000UV and no fasteners. 3M 4000 has about the same adhesive capability as 4200 but with more UV protection. I dug out the balsa core in the deck around the hole I cut the day before. I only needed to cut back about 1/4" since there would be no fasteners penetrating the deck. I coated the balsa with unthickend epoxy and followed with epoxy thickened with cabo-sil. After it was hard taped off the hole and trim ring and I applied 3M 4000 to the bottom of the trim ring and pressed it into position. I used a "Dap Cap" to clean up the excess, removed the tape that protected the teak trim ring, and cleaned up the excess with alcohol.
Next, I went back to work on the trim ring. As detailed in a previous post, I cut the trim ring from the square lamination I made on a band saw. Now I needed to cut a 4 3/4" hole through the trim ring for the deck flange to plug into. I hate buying one time tools. But there was no reasonable way around it. I bought a Lenox 4 3/4" hole saw. I saved a few dollars as it came without the arbor but since all my other hole saws are Lenox I was able to use the arbor from one of them. I decided I needed to cut the hole before I beveled the trim ring to match the deck. It was the only way to ensure it would be vertical. It took a while but I was able to cut it on my bench top drill press. First I drilled a 1/4" hole al the way through the center and out the other side. Then I used the hole saw to cut half way through the plug--all the way to the bottom of the hole saw. I flipped the plug over and using the 1/4" hole as a guide I cut back through all the way to the bottom of the hole saw which just made it through. A perfect hole. Next, I took the trim ring up to the boat and used some wood scraps to prop the outside edge up so that it was level on top. I then scribed around it with a compass. I used a power planer to cut most of the excess away. Then, I used a block plane and spoke shave to trim to the scribed line. It fit perfect. I was pleased. It made me realize how much I have learned during the rebuild as the did not require days of research and planning . . . it took maybe 45 min. Next, I took the hole saw up to the boat and after taping off the area I needed to cut through (to protect the gelcoat) I cut a matching 4 3/4" hole through the cabin top. I checked the fit of the trim ring over the hole. They lined up perfectly. I finished up the day by rounding over the top and inside edge of the trim ring with the router. Next day, I cut a caulking grove in the bottom of the trim ring to provide a place for caulk to lay and not get completely squeezed out. I developed a couple of options for securing the trim ring to the cabin top. In the end I went with the simplest of the options as suggested by someone I trust. I used 3M 4000UV and no fasteners. 3M 4000 has about the same adhesive capability as 4200 but with more UV protection. I dug out the balsa core in the deck around the hole I cut the day before. I only needed to cut back about 1/4" since there would be no fasteners penetrating the deck. I coated the balsa with unthickend epoxy and followed with epoxy thickened with cabo-sil. After it was hard taped off the hole and trim ring and I applied 3M 4000 to the bottom of the trim ring and pressed it into position. I used a "Dap Cap" to clean up the excess, removed the tape that protected the teak trim ring, and cleaned up the excess with alcohol.
Below:
1. I used a 4 3/4" hole saw to cut the hole.
2. I scibed a line that matched the slope of the cabin top.
3. I used a hand power planer to cut the excess wood away.
4. I finished trimming with a block plane and the fit was excellent.
5. Another view. The 1/8" hole marks the center of the hole.
6. The reflecks deck flange with the smoke head attached. The flue fits inside the inner ring and the out ring is part of the heat shield.
7. Another view.
8. Test fitting.
9. Drilling the 4 3/4" hole in the cabin top.
10. Another test fit.
11. I cut the caulking grove with a cove bit on the bench top router.
12. I trimmed back the balsa core then coated it with until thickened epoxy.
13. Then, I filled the cavity with thickened epoxy to ensure no water can get to the balsa core.
14. I used 3M 4000UV to mount the trim ring to the cabin top.
15. Protect complete. I will drill and install the screws once I have the heater and flew in position and the overhead panel reinstalled.
I completed the installation of the flue for the Refleks heater. I don't know if this is the final design but it is pretty close. I decided to start with the flue pipe as long as possible to the upper 45 degree elbows. A long straight flue is supposed to create a better air flow and reduce sooting and the likelihood of a back draft. It also helps keep the elbows out of the way and create a less cluttered look. I have a smaller piece of flue pipe so if I decide to shorten the pipe and lower the elbows a little I have the pipe to do that. I may need to add a little shielding next to the cabin side in the area of the elbows but I'll wait till I run the heater this fall to be certain. I started by drilling a hole the overhead panel after taping it off. I followed that will the 4 3/4" hole saw from the inside up. Then, I removed the panel and coated the end grain around the hole with a couple of coats of epoxy. Next I reinstalled the panel. Then, I cut the flue pipe to length. Finally, I installed the pipe. The photo has a little optical illusion to it as it makes the assembly look a little distorted but it is perfectly plumb and square. I need to come up with a design for then inside trim. I think it is important to incorporate additionally shielding inside the hole to reduce heat transfer to the overhead panel and the cabin top around the edge of the cut out. I'll set that aside for later though since I don't need to drop the overhead panel to install it.
Flue installed.
The 10 Gallon kerosene fuel tank that supports both the Refleks heater and the nav light and oil lamps arrived yesterday. After researching several tank builders Luther's Welding seem to meet my needs the best. They have a good reputation, responded to all of my emails, worked with my design requirements and gave be a pretty good price. The tank will be positioned vertically on the cockpit locker side of the aft bulkhead that separates the Q-berth from the cockpit locker. It will be mounted 'thwartship. The fuel line is in the bottom of the tank as the system is gravity feed. I will install a pet-cock to shut off the flow of fuel. The tank has a baffle. On the top there is a fuel cap, inspection plate, and vent nipple. The tank will be filled by opening the cockpit locker and unscrewing the cap. It is perfectly in line with the refleks heater which is also on the starboard side of the boat so the heater should work equally well on each tack. Though I would have liked for the tank to be in the 15 gallon range this was as big as the location would resonably accomodate. I'll carry some additonally kero in a 5 gallon on a rack in one of the cockpit lockers if necessary.
While waiting for the finish to dry on the hull ceiling I went back to work on installing the kero tank in the starboard cockpit locker. A couple of days ago, I applied foam wedges and epoxy tape to the bulkheads and deck in the port locker. This is another example of shoddy workmanship. there was at least a one inch gap above both bulkheads and the deck and no bonding in place. To install it, I traced the tank and flanges onto a piece of door-skin ply. I cut the template out with my jig saw and then clamped the tank to the template. I drilled holes through the template to align perfectly with the holes in the tank. Next, I took the template into the locker and crammed myself into this very tight spot. This is the main reason why I have not yet bedded and fastened the teak locker coamings in place . . . it is much easier to get in and out of the locker when they are removed. Note to self: You should not have a locker on your boat that is so small you can't crawl inside to perform work. With the template in place I drilled 1/4" holes through the template and through the bulkhead that separates the locker from the quarter berth. Previously, I very carefully measured to make sure I would not drill into anything important on the quarterberth side of the locker. I drilled a hole, inserted a 1/4" bolt, drilled another hole, inserted another bolt and so on and so forth. By inserting the bolts as I went I reduced the chance that the holes would not line up properly due to some hidden error that could compound itself. I removed the bolts and template and placed the tank in position. The bolts fit perfectly. In the photo, you can see the vent tube on the inboard top side of the tank. The vent line will penetrate the deck and be secured along the outboard side of the cockpit coaming. Next, I built a template for a shelf from doorskin strips and a hot glue gun. I then cut and test fit a plywood cleat in the port locker that would support the template shelf. The shelf will make the locker much more useable by providing a flat surface on the bottom of the locker, otherwise the steep slope would cause anything placed in there to slide under the kero tank. Satisfied with the fit, I taped the cleat in place with 1708 biaxial and West Systems Epoxy. I still have to add another cleat to the inboard side of the locker so the shelf will be fully supported. I could have epoxied the shelf in place, but then I would have to cut it out to remove the tank. This approach will allow me to remove the shelf by unscrewing it from the cleats so the tank will have enough room to be rotated and passed up through the locker opening. I will also build some shelving along the outboard side of the locker as well. Once all the construction is completed, the tank will be removed and the locker will be painted with grey Interlux bilgekote paint. Then, the tank will be reinstalled.
Foam wedge and two layer of 1708 biaxial and West System Epoxy to bond the bulkhead to the underside of the deck.
The drilling template for the kero tank.
The kero tank temporarily bolted in place with (8) 1/4" bolts. Note the vent on the right top of the tank. That will eventually be led to the ouboard side of the cockpit coaming.
This is what the tank looks like through the top of the locker. It can be filled without going into the boat.
In order to finish up the starboard locker so it is ready for painting I needed to drill the hole in the aft bulkhead for the fuel line that runs from the kerosene tank to the reflecks heater. I recently purchased the brass shutoff valve and appropriate hose barb and coupling so this seemed like a good time. The bulkhead in the photo is at the foot of the quarter berth. I drilled the hole from both sides with a 2" hole saw. Then, I routered the hole with a 1/4" round over bit. The only way I can reach the shut off valve is to remove the bottom shelf in the locker. Then, it is a simple matter to reach under the tank and rotate the valve. I'll add a split hose to protect the fuel line from any chafe that might occur as the line passes through the hole.
The hole for the fuel line lined up nicely. There is a little bit of an optical illusion in the photo.
I needed to install a wood pad around the opening for the Refleks heater flue pipe. I wanted to keep direct heat away from the closed cell insulation even though it is fire retardant. There will be a metal heat reflector sleeve installed as well. This was a necessary step before I could install the trim around the overhead panels.
To complete the flue assembly for the Refleks kerosene heater I needed a heat shield for the deck collar. The deck plate head shield only extends about 1 1/2" below the deck surface. The deck plate sits on a scribed teak deck pad about two inches high. The deck is about an inch thick, then there is an air gap between that and the overhead panel, and then there is another scribed mahogany pad on the inside of the cabin. Those interior surfaces need a heat shield to protect them from the high temps that will occur inside the flue. Last week I made a mock up of what I wanted and took it to a local fabricator. I think they did a very average low end kind of job. I was not happy but that was the best I was going to get from them. I had planned to just screw the shield to the inside pad and be done with it. But, it was not up to our standard. So, I thought about it for a little while and decided I could cover it with a teak trim piece. I traced the shield out and then use a trim bit in my small trim router and cut out the area to be recessed, just like you would mortise a set of hinges. Then I screwed the interior pad to the overhead, the shield to the pad, and the trim piece over the shield plate with some bronze oval head screws. I will eventually varnish the pad but leave the teak bare. It looks good.
Below:
1. This is the heat shield upside down with the teak trim piece next to it.
2. I mortised the underside of the teak trim to fit over the flange of the head shield.
3. This picture depicts the three parts that make up the assembly.
4. The shield has to be almost six inches long to provide adequate protection for the interior overhead, the trim pads, the deck, etc.
5. The interior trim pad in place. It will eventually be varnished.
6. The heat shield being slide into position.
7. The flue will pass through the hole and fit into the deck plate and smoke head.
I had been wondering where I would install the tap for the kerosene for a long time. The kerosene tank, located in the starboard side cockpit locker, runs directly to the Refleks heater which is located at the forward end of the saloon on the starboard side. I wanted to install a tap on the fuel line so that I can more easily fill our kerosene nav lights and interior lamps. I did not want to have to deal with the lamp, funnel and a separate fuel can trying to keep all three under control while the boat is rolling around.
The tap on the fuel line between the kerosene tank and the refleks heater.
Along with the other trim that we varnished was the platform and the V groove panel that supports the Refleks kerosene heater. I am very pleased with how they turned out. I think, after some early learning struggles, I have become a competent varnisher--of course it took about four gallons of varnish to get to this point. To install the vertical panel I had to add a small wedge section of walnut and then cut it back to allow the panel to drop down next to the walnut. All of the V groove panels sit on the same bearing surface that support the sole. The sole butts up to the v-groove which allows any water to drip down pass the sole via the grooves. The v-grooves also allow air to circulate around the boat. If you look closely in the photos, you can just tell that the v-grooves extend down (7/8"" below the top surface of the sole. The counter tops are the same way.
The refleks heater sits on this platform.
Installing the Kerosene Tank Vent. I completed the installation of the kerosene fuel tank. I had to add a vent tube (photos below). There were not many place to install it. When I designed the tank I had already determined this was the best option availble so this was not a surprise. It was the plan all along. I drilled down through the side deck, next to the cockpit coaming and just aft of the primary winch pad. The tank vent hose barb was directly below. I over drilled the hole and then filled it with epoxy. After it cured, I drilled a 5/16" diameter hole through the epoxy plug and chamfered the hole. I applied some Teff-Gel to the washers and installed the 1/4" bolts through the aluminum tank flanges and bolted it in place to the bulkhead on the aft end of the quarterberth. Next, I used a piece of 1/4" copper tubing and bent it to a "U" shape and test fit it down through the hole I drilled in the deck. I had to install a teak spacer block since I could not get the hole next to the coaming as the deck mold was recessed down for the coaming to bolt to. I needed copper straps to secure the vent tube in place. I used a hack saw to cut 3/8" wide sections from a 1" diameter piece of scrap copper pipe. I split them and heated them up. While they were glowing hot I hammered them flat, bent them around the copper tube, and then quenched them in cold water. I drilled holes in the end then secured them to the teak spacer block with bronze screws. After test fitting I bedded the teak block with Dolphinite. I caulked the chamfered hole the copper tube passes through with Boat Life polysulfied. It's not a perfect solution but I am satisfied with the look and how it blends in with the rest of the boat. Last, I installed a short section of Trident fuel line to connect the tank to the copper tube and secured it in place with SS hose clamps. Once I install the teak wood plugs the project will be complete.
Below:
1. I drilled and over sized hole, filled it with epoxy, and then drilled a hole through it when it was cured.
2. I used a piece of scrap 1/4" diameter copper tube and a teak spacer block.
3. I bedded the block with dolphinite and made the straps by cutting off slices of copper from a 1" copper water pipe.
4. The tank vent hose barb to the copper vent connection.
While working on the water tank hold down system I also did a little work on the refleks heater. The regulator has three fittings on it. One is the fuel line "inlet". One is the fuel line outlet--it goes from the regulator to the burner pot. And, the third is on the underside of the regulator and is an overflow outlet. The directions for installation very clearly state that the overflow outlet is an important safety feature that many people dangerously cap off. The purpose of the outlet is to allow any excess fuel that might collect in the regulator to flow out of the regulator and into a separate container. The trick is to figure out how /where to run the line since it needs to be below the heater and accessible. I have been thinking about this for some time and finally decided to connect a rubber Trident fuel line to a copper tube attached to the overflow valve and run forward and to a collection bottle in the bilge adjacent to the heal of the mast. It will be easy to see and easier to collect and return to the main tank should the need arise.
Looking under the platform that supports the refleks kerosene heater.
Finally, it was time to start up the heater. I had to fuss with the fuel line for a few hours as the fuel did not want to run through the fuel line, fuel filter, past the diverter line and separate pet-cock, and to the heater regulator. After a little while I finally came up with the right combination of steps to bleed the air from the line. Starting the heater up was an interesting experience as the directions don't provide a lot of info--they are translated from Danish to English. The key, however, is to start with good fuel. I started using Sunnyside Pure A1 Clear Kerosene a few months ago to solve some issues with my cabin lights. I found it at our local hardware store. What a difference over standard died kerosene I used in round which heater we use on occasion in our garage. Absolutely smokeless. Very little to no odor when burning.
Pure clear kerosene improves performance dramatically. I experimented with a gallon of fuel to make sure it was of good quality. Then, I bought it in five gallon cans and saved about 15 percent.
Looking down onto the cast iron cook top there is a small hole. Looking into the hole you can see the flame in the fire box and you know the fuel is burning.
To run the heater, I opened up both ends of the shed and the transom hatches to make sure the exhaust would vent out of the shed. I admit I had a brief vision of the shed catching fire from a run-away heater and burning down around the boat. But, now was the time to test it so I shook that vile thought off and pressed ahead. Since our heater regulator was set by the factory for kerosene (paraffin), vice the standard diesel, I started off by lighting it using just the kerosene in the drip pot. It worked OK but was a little finicky, smoke some, and made some "woofing" noises that were kind of frightening, though, it finally smoothed out. I ran it for 45 min and shut it down. I varnished some wood then when back and tried it again using the directions for diesel fuel heaters and poured in 5cc of denatured alcohol then set the regulator to "pilot" allowing the oil to mix with the alcohol. I used a small piece of paper towel which I lit and dropped down the top (with the cast iron cook top removed). The flame lit, but I did not like this technique at all. Lots of smoke and more woofing noises as it heated up. I shut it down. Today, I took the regulator apart. Very simple to do. I wanted to know how the adjustments work. The "pilot" setting looked to me like a max setting and nothing more. I reassembled the regulator. Then, I experimented by looking into the drip pot while I turned the regulator to different settings and timed how much and how long it took the fuel to flow into the pot. That knowledge helped me come up with another approach. This time I poured in 5cc of denatured alcohol keeping the regulator off and lit it. I let it burn for six minutes, with the cook top off, making sure the fuel pot and coil basket were good and red hot. Then, I opened up the regulator to the lowest setting and put the cook top back in place. That did the trick. It ran like a champ. I am not convinced it is the best way to light the heater but for now it gets the heater running with minimal fuss and practically no smoke or weird noises. I ran the heater for five hours today. It ran smooth without any hiccup. I checked on the fuel fittings from the tank to the regulator looking for leaks but everything was tight and dry. There was no smoke of any kind coming off of the smoke head. After it cooled, I removed the cast iron cook top and looked inside. No soot of any kind. That's impressive.
The M-66MK may only be rated at 5500 BTUs but it puts out some serious heat. At the lowest setting it quickly got up to about 350F-375F. After watching it for a while, I set the regulator to position 3 of 9 settings. The temp quickly climbed to about 455F. The wood behind the heater, that is to say, on the starboard side of the boat was warm, but not hot even when the heater was at 450 degrees (there is the largest air gap on that side). However the wood on the forward side of the boat, the main bulkhead side, was very hot to the touch (there is a much small air gap on this side). But it was hot only over about 12-15" of vertical distance--half extending below the cook top level and half above. The wood was barely warm near the flue all the way up to the deck head. It is clear to me that I will need heat shielding. I'll do some more experimentation to determine how much shielding I need and exactly where it will need to be positioned.
At the lowest setting the stove top is about 375F or about 185C.
At setting 3 of 9 the temp is about 450F or 260C.
My initial thought is to install a 90 degree wrap-a-round polished SS heat reflector that is about 15" tall that extends about 7.5" above and below the level of the cook top and follows along the forward bulkhead, turns 90 degrees and extends back along the starboard side behind the heater. I don't think I need any for the flue. I'll need to find a source for the heat shield. I also need to gather some info and send it off to Refleks to see if they recommend another way to start the heater given that it is metered for kerosene vice diesel fuel. I am impressed with the heater so far. Lots of heat. I plan to order an Eco fan to put on the cast iron cook top and better distribute the heat.
I visited various metal fabricators looking in to SS sheet metal. I called the tech lines for Force 10 and Dickinson Stoves. I made some mock ups. The tech rep at Force 10 told me I would not need spacers. The SS directly on the mahogany would be fine. He informed me that the SS is really relying on its reflective capabilities and if polished will be more than up to the task. That was news to me. The both though polished aluminum would work as well though it might be susceptible to warping at the thinner gauges. The general consensus seems to be that polished 20-22 gauge SS would be about right. Anyway, no decision yet. I also spent a lot of time trying to eliminate an air block between the kerosene tank and the ball valve tap under the companionway ladder . . . the fuel flowed fine to the heater (down stream from the ball valve) but only trickled out the ball valve tap itself. After a lot of fussing, draining, etc, I decided that there simply was not enough head pressure to drive the air out of the line between the "T" off the main line up- hill to the ball valve, though it was below the bottom level of the tank. So, I spent a few hour reconfiguring it slightly by eliminating the "T" and uphill climb to the ball valve. The line now runs from the tank to a "T" directly on the back side of the ball valve then straight to the heater that is low enough in the boat there is plenty of head pressure for the rest of the line. Works great. The EcoFan model 810 arrived and I tested it a couple times on the top of the Refleks heater. Though the tests were limited, I am impressed. It moves a fair amount of air and it is whisper quiet. A very neat device that I think enhances capability of the heater. Below, there is a movie clip of it in action.
I visited various metal fabricators looking in to SS sheet metal. I called the tech lines for Force 10 and Dickinson Stoves. I made some mock ups. The tech rep at Force 10 told me I would not need spacers. The SS directly on the mahogany would be fine. He informed me that the SS is really relying on its reflective capabilities and if polished will be more than up to the task. That was news to me. The both though polished aluminum would work as well though it might be susceptible to warping at the thinner gauges. The general consensus seems to be that polished 20-22 gauge SS would be about right. Anyway, no decision yet. I also spent a lot of time trying to eliminate an air block between the kerosene tank and the ball valve tap under the companionway ladder . . . the fuel flowed fine to the heater (down stream from the ball valve) but only trickled out the ball valve tap itself. After a lot of fussing, draining, etc, I decided that there simply was not enough head pressure to drive the air out of the line between the "T" off the main line up- hill to the ball valve, though it was below the bottom level of the tank. So, I spent a few hour reconfiguring it slightly by eliminating the "T" and uphill climb to the ball valve. The line now runs from the tank to a "T" directly on the back side of the ball valve then straight to the heater that is low enough in the boat there is plenty of head pressure for the rest of the line. Works great. The EcoFan model 810 arrived and I tested it a couple times on the top of the Refleks heater. Though the tests were limited, I am impressed. It moves a fair amount of air and it is whisper quiet. A very neat device that I think enhances capability of the heater. Below, there is a movie clip of it in action.
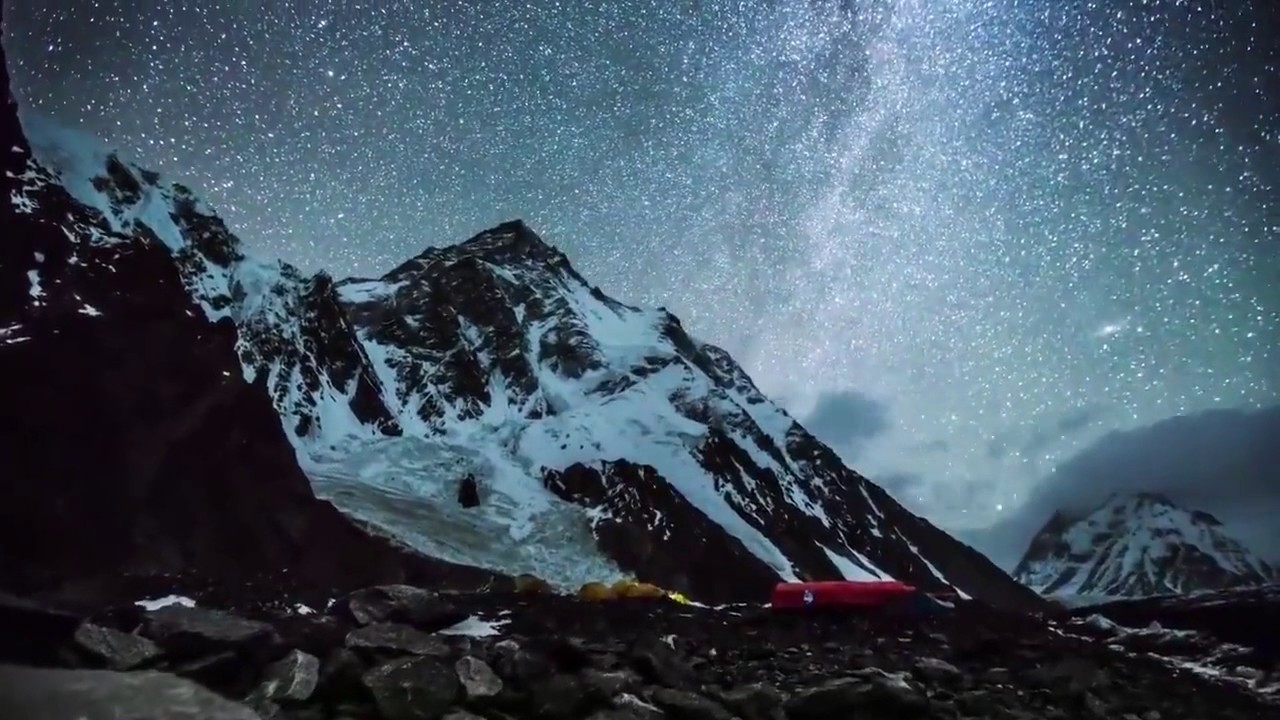
Video can’t be displayed
This video is not available.
Link currently not working
The fan seems to be pretty secure on the stove top, though I will need to come up with a handsome way to secure it in place yet be easy and quick to move. I like the fact that the fan can be easily reoriented in just about any direction desired. While using the sitz tub the fan can be turned to blow warm air towards the tub . . . or across the cabin to the opposite settee . . . or back towards the aft end of the boat.
2 Jan 15I mailed off the patterns for the lee cloth hooks to Mystic River Foundry. I hope to hear back from them next week. Today, I sewed a bag for the parachute storm anchor. Nothing fancy. In fact, I used material from and old sail bag along with some sunbrella scrap. I reinforced the bottom, added a nylon retention strap, and a draw string. Hopefully, we will never need to employ it. I ran the heater some today and experimented with some shielding options. I attempted to determine if what the Force 10 tech rep I talked to last week told me was accurate--that I did not need to provide an air gap, I could put the SS shielding on the wood without spacers. I used some aluminum foil and taped it to the surrounding wood where I had previously determined that the wood got hot. Surprisingly, the wood behind the foil, even though it was in contact with the wood, remained cool while the wood just above and below the foil was warm. Interesting. I also took some heater top temperature measurements with the fan running. With the Refleks heater on the lowest setting the heater ran about 200 degrees. Without the fan, the top of the heater measured 375 F. With the heater set to level 3, it measured about 275 F vice 450F. So, I decided to set heater to level 7 of 9. It measured about 325 F and I estimate that without the fan it would have been about 500F. I did not want to run the heater that high without the fan as I knew the wood would get very hot. At setting 7 the fan was blowing an impressive amount of heat across the boat. It was not that cold today so I don't know what the "felt" effect would be with colder temperatures but my instincts tell me the fan will significantly (?) contribute to moving hot air across the boat reducing cold spots and creating a more consistent temperature. These are of course, just preliminary impressions. I had no trouble starting the heater. It fired right up, burning clean and clear from the start.
2 Jan 15I mailed off the patterns for the lee cloth hooks to Mystic River Foundry. I hope to hear back from them next week. Today, I sewed a bag for the parachute storm anchor. Nothing fancy. In fact, I used material from and old sail bag along with some sunbrella scrap. I reinforced the bottom, added a nylon retention strap, and a draw string. Hopefully, we will never need to employ it. I ran the heater some today and experimented with some shielding options. I attempted to determine if what the Force 10 tech rep I talked to last week told me was accurate--that I did not need to provide an air gap, I could put the SS shielding on the wood without spacers. I used some aluminum foil and taped it to the surrounding wood where I had previously determined that the wood got hot. Surprisingly, the wood behind the foil, even though it was in contact with the wood, remained cool while the wood just above and below the foil was warm. Interesting. I also took some heater top temperature measurements with the fan running. With the Refleks heater on the lowest setting the heater ran about 200 degrees. Without the fan, the top of the heater measured 375 F. With the heater set to level 3, it measured about 275 F vice 450F. So, I decided to set heater to level 7 of 9. It measured about 325 F and I estimate that without the fan it would have been about 500F. I did not want to run the heater that high without the fan as I knew the wood would get very hot. At setting 7 the fan was blowing an impressive amount of heat across the boat. It was not that cold today so I don't know what the "felt" effect would be with colder temperatures but my instincts tell me the fan will significantly (?) contribute to moving hot air across the boat reducing cold spots and creating a more consistent temperature. These are of course, just preliminary impressions. I had no trouble starting the heater. It fired right up, burning clean and clear from the start.
With the fan running the heater top was 200F vice 375F.
With the fan running, the heater top was 275 vice 450F.
Setting 7 of 9. I estimate the heater would be over 500F without the fan running.
I cut a 4" diameter hole in the fore and aft bulkhead that runs along the underside of the cockpit foot well on the starboard side (from the old engine compartment into the starboard cockpit locker). The hole allows me to have direct access to the fuel shut off ball valve that I previously only had to access to through the top of the cockpit locker. My arms were just barely long enough to reach under the tank and to the valve, if the locker was empty. Neither Gayle nor the kids could reach it. Previously, I installed a clear fuel filter just forward of the ball valve to filter the fuel somewhat and to allow visual inspection of the fuel. It was a simply install and by shutting off the ball valve it is easy to disconnect, clean, and reinstall.
I added a clear fuel filter to better assess the condition of the fuel.
I cut a hole through the fore and aft bulkhead so I have direct access to the fuel tank shut off ball valve.
After I decided what I want to do for whielding I off a 4" diameter 316 SS flue with Torch at Torch's Custom Fabrications. Torch is a great guy and a real pro. He builds custom motorcycles. He is a retired Marine who spent most of his career as a welder. He has a ton of experience and a complete fabrication shop with with all kinds of milling machines and lathes, etc. In order to get a half shield to fit around the 2 3/4" diameter flue with the desired stand-off we needed a larger pipe to start with, thus the 4" diameter one I purchased. Torch cut it in half length wise then welded small SS brackets on to it then welded them to the 2/34" diameter flue pipe. You can just make out how it was accomplished in the first photo below. He did a really nice job of polishing up the original flue so the whole thing matches the other highly polished components. He ground a radius on the corners as well. I think it looks terrific. Today, I completed the installation of the heat shield for the heater as well as for the galley stove. Afterwards, I ran the heater wide open (500 degrees F) with the Ecco fan running and without to test the effectiveness of the shielding. The wood area behind the flue shielding remained cool to the touch throughout the testing. I used #6 SS pan head screws for the 6 3/4" x 13" long shield just forward of the heater. I off set it from the bulkhead about 1/8" because I wanted the edge of the shield to overlap the walnut trim as it also got hot during initial heat testing and the trim is proud of the mahogany about 1/8". This provided a nice even look. This shield also worked very well. The only area that was warm to the touch was the small 7" wide cutout that is just above and outboard of the arm rest when you are sitting on the forward end of the starboard settee. I'll add a small piece of reflective shielding which you won't be able to see unless are looking aft from the head compartment. The other shield is visually blocked by the Ecco fan when it is sitting on the top of the heater. At this point, I am pleased with the Refleks heater. I have a pretty good feel for out it works. I have taking it apart to include the regulator. I know how to start it quickly, efficiently, and with little to no fuss. It burns clean and hot. I also drilled the holes and ground a radius on the corners for the heat shield above the galley stove. I used # 6 SS pan head screws for this shield as well. The installation for the galley stove shield was pretty straight forward. You can't see it unless you get down very low and look up under the bridge deck above the stove. The back burners just barely overlap the bridge deck and I don't expect any issues there.
In this photo you can see how the heat shield was fabricated and welded to the main flue pipe. I will need to add a small piece of shielding to the area to the right of the photo that still gets warm when the heater is running wide open.
The half shield on the flue is barely noticable.
With the Ecco fan on the reflecks heater top the SS heat shield on the bulkhead is not very visible.